A warehouse is a planned space for the storage and handling of goods and material. (Fritz Institute)
In general, warehouses are focal points for product and information flow between sources of supply and beneficiaries. Warehouse management is very complex. This is true to the degree that it’s a more focused and detailed system for the operations in a business’s warehouses. Management systems will typically divide warehouses into many compartments and bins, allowing specific items to be located in a specific area of the warehouse when needed.
Warehouse management is not just about locating items, however, it also quite controls what happens in the warehouse. For example what actions warehouse staff is taking and when, how items are storing and treating, and what processes are to be used for different items in the warehouse. Some systems integrate warehouse management software with equipment such as forklifts, packaging machines, and conveyor systems, making the warehouse even more streamlined and efficient.
In today’s fast and competitive world, delivering your products on time and with multiple channels can be pretty challenging. You receive continuous burden from numerous buyers and store locations. To handle a successful warehouse is not simple and easy. It is a challenge to keep up with inventory demands while monitoring the inventory process and the needs of your workers and your customers or buyers.
Deprived of going into the disadvantages of inventory reduction and out of stock situation, but focusing on a businesses’ ability to fulfill all the requirements brought in by customers. This is why your business needs to have a proper inventory management practice, as things can quickly go wild if you’re not careful managing the inventory process. With that in mind, here you have some of the best ideas that will make warehouse inventory management run smoothly.
Important Procedures of Warehouse
You should know about some important procedures of how the activities in the warehouse should be carried out and clearly defines the processes to be adopted. These can be adopted as ‘best practice’.
The procedures will normally provide the step by step guidance on how to manage each aspect of warehousing and may cover:
- receiving and issuing of supplies;
- quality control or verification;
- storage of goods;
- how to control stock movement (stock control);
- documentation flow;
- how to detect and deal with stock losses;
- how rejected material will be managed; and
- how to deal with unwanted material, obsolete and scrap, disposal.
These important procedures are critical to the overall accuracy of your company’s inventory and for the warehouse. And without any doubt no warehouse system cannot be run successfully without an automation.
Make sure inventory reaches the shelf in the shortest amount of time; “out of stocks” are significantly reduced. Looking that electronic put away orders to provide exact location and in most efficient route. Rapidly scanning location labels to ensure items are put-away correctly. Conducting inventory in real-time is also very important for the warehouse management. Performing quick and accurate cycle counts are crucial. Removing motion, waiting and transportation waste.
Automating your warehouse systems makes a huge impact
Your operations are growing and your labour costs are increasing. Management wants you to do more with the same amount of money (or less) next year. You need to find ways to keep costs down while improving your operations at the same time. What can you do?
Automating your warehouse systems can make a huge impact on your operations including, but not limited to, these six ways:
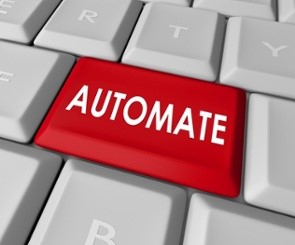
Real-time inventory information
In a typical manual warehouse, inventory data is always out of date. By the time a warehouse worker gets a pick ticket, retrieves the product, and manually enters the information into the manual inventory tracking system, the numbers are generally already inaccurate. With an automated system, however, there is no delay in updating the inventory management system. When a worker picks a product, that information is automatically instantly relayed to the WMS system and updated in real-time.
Improved storage space capacity
When you implement warehouse management software, you may find that you could have been fitting more product onto your shelves! The WMS assigns every product a specific location and bin number in the warehouse, based on the size of the bins and the amount of product kept in inventory. The lesser used inventory is often assigned to higher shelves or in out-of-the-way places within the warehouse, while the more popular items can be kept on lower shelves and near the shipping area. This approach maximizes the use of your warehouse shelves and allows you to be more efficient within the your allotted space.
Reduced energy use
With exact locations provided by the warehouse management system, and the most popular items assigned closer to the packing/shipping areas, warehouse workers can pick orders faster and without the excessive need to go to remote parts of the facility. This preserves physical energy and reduces the unnecessary use of fuel for forklifts. The strategic location-assigning could also allow for a reduction in the amount of electrical energy needed, as areas of the warehouse that are storing slower velocity items could use less lighting or climate control (depending on stock type).
Reduced product damage
Implementing an automated warehouse management system means product will need to be handled using strict procedures. Predictable, consistent handling of products will dramatically reduce the amount of risk for damage and waste produced within the warehouse.
Reduced injuries and claims
Automation helps maximize the efficiency of any warehouse operation over time. By providing smoother, more predictable operations and helping to streamline storage, retrieval, and packing efforts, most warehouses experience a reduction in employee injuries and thus fewer workers’ comp claims as well as fewer lost days to on-the-job injuries. This benefits both the employer and the employees.
Improved warehouse efficiency
Modern warehouse management software packages give warehouse managers the ability to identify inefficiencies and address them. They show how long it takes an average warehouse worker to pick orders. They also show which workers are most efficient and which ones need extra training. Additionally, they identify which products are bestsellers and which ones barely move, which helps improve warehouse layout and pick paths.
Each of these benefits show why automating your warehouse systems is a good idea. While the initial set-up of the warehouse management software and equipment will take some effort, in the long run you will have improved operational efficiency along with notably reduced costs.
And definitely many more benefits including space savings, lower building costs, improved productivity, more efficient material flow, less people, safer operations, reductions in inventory, increased reliability, reduced running costs, better ROI and lowest lifecycle cost.
References
http://dlca.logcluster.org/display/LOG/Warehousing+and+Inventory+Management
http://www.newcastlesys.com/blog/7-best-practices-for-inventory-management-for-warehouses